Quality checks are made by artificial intelligence
IDS USB 3 cameras were chosen for crack and micro-crack detection of caps by the company APREX Solutions for a production line they developed. The industrial USB 3 camera offers very good image quality and very quiet performance. The so-called “SOLOCAP application” was trained with artificial intelligence using APREX Track AI software.
Strong price pressure combined with high quality requirements – the beverage and bottle industry faces the classic dilemma of many industries. This is also the case in the quality control department of a French manufacturer of plastic caps. Reliably detecting cracks and micro-cracks on plastic caps in 40 different colours and shades running at high speed on a production line is a real challenge. APREX Solutions from Nancy, France has successfully achieved this goal with the help of image processing technology and artificial intelligence. The basic images are provided by a USB 3 industrial camera from IDS Imaging Development Systems. SOLOCAP is a subsidiary of La Maison Mélan Moutet, manufactures all types of plastic caps for the food sector at its industrial site in Contrexéville. Among them, a top-class screw cap suitable for any glass or PET bottle. Thanks to a clampable lamella ring arranged around the bottle collar, it enables simple, fast, absolutely tight and secure seal. However, the slats must be reliably and extremely carefully checked for cracks, tears and twists during production. This is the only way to guarantee absolute tightness.
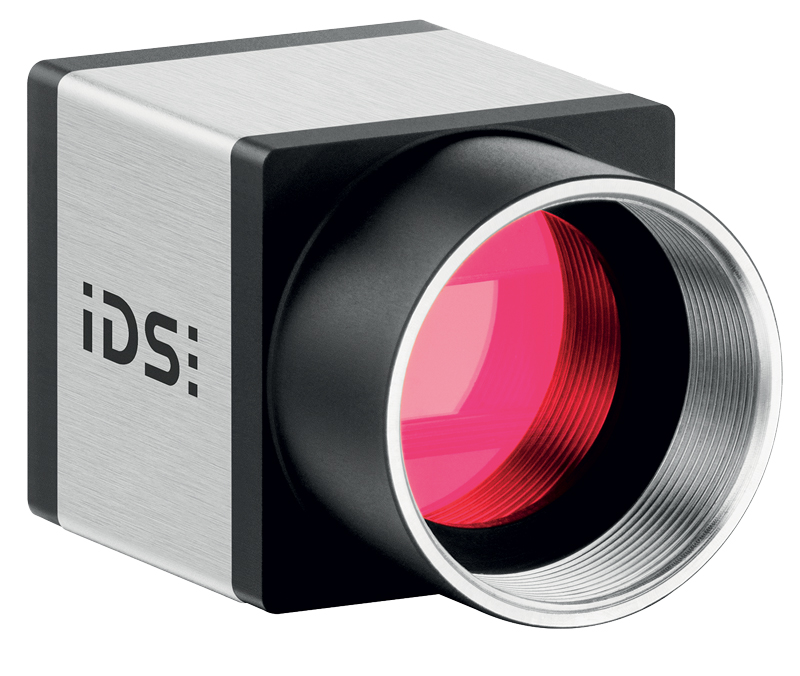
In-house software algorithms
The previous inspection system could not meet these high requirements. APREX Solutions realised the new solution with artificial intelligence individually on the basis of in-house software algorithms. The necessary specifications were developed in advance in cooperation with the customer. This also included several inspection stages, one of which, for example, was the reject control to avoid false reports. The introduction took place in two phases.
First, the specific “SOLOCAP application” was trained with the help of the intelligent APREX Track AI solution. The software includes various object detector, classifier and standard methods that operate at different levels. Networked accordingly, they ultimately deliver the desired result tailored to the customer. Four control levels with several test points guarantee a reliability rate of over 99.99%. In the second step, this application was implemented in the production line right after the first assembly run with APREX Track C&M. The latter was specially developed for the diverse image processing requirements in the industrial sector. This includes, among other things, the control and safeguarding of a production line up to the measurement, identification and classification of defects in the production environment. The software suite delivers the desired results quickly and efficiently, without time-consuming development processes. After a short training of the AI methods, the complete system is ready for use at the customer. In the case of SOLOCAP, it combines an IDS UI-3280CP-C-HQ industrial camera, powerful ring illumination and a programmable logic controller (PLC) to provide comprehensive control over all inspection processes. At the same time, it records all workflows in real time and ensures complete traceability. Only one camera is needed for this. However, APREX TRACK C&M could handle up to five cameras. The difficulty of this project consisted mainly in the very subtle expression of the defects we were looking for and in the multitude of colours. With APREX’s software suite, it was possible to quickly set up an image processing application. The image from the camera provides the basis for the evaluations. It captures every single cap directly in the production line at high speed and makes the smallest details visible to the software.
One crucial component: the camera
The UI-3280CP-C-HQ industrial camera is integrated into the system with the 5 MP IMX264 CMOS sensor from Sony. The USB 3 industrial camera provides high image quality with low-noise performance – at frame rates up to 36 fps. CP stands for “Compact Power”. This is because the tiny powerhouse for industrial applications of all kinds is fast, reliable and enables a high data rate of 420 MB/s with low CPU load. Users can choose from a large number of modern CMOS sensors from manufacturers such as Sony, CMOSIS, e2v and ON Semiconductor with a wide range of resolutions. Its innovative, patented housing design with dimensions of only 29x29x29 mm makes it suitable for tasks in the fields of automation, automotive, medical technology and life sciences, agriculture, logistics as well as traffic and transport, among others. Screwable cables ensure a reliable electrical connection. Thanks to the IDS-characteristic plug & play principle, the cameras are automatically recognised by the system and are immediately ready for use.
Requirements for product safety, but also for reject control, especially in the case of false reports, were quickly met. AI offers quality assurance, but also all other industries in which image processing technology is used, new, undreamed-of fields of application. It makes it possible to solve tasks in which classic, rule-based image processing reaches its limits. Thus, high-quality results can be achieved with comparatively little effort – quickly, creatively and efficiently.