MACCHINE
COMPONENTI
UTENSILI
SOFTWARE
METROLOGIA
ECONOMIA

L’industria manifatturiera del futuro
Il 28 marzo scorso, presso il Palazzo delle Stelline a Milano, si è tenuto l’European Tooling Forum, organizzato da ISTMA World, European Tooling Platform e UCISAP.
CONTROLLI
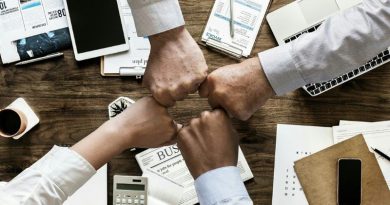
Una partnership vincente con il CNC Z32 di D.ELECTRON
CTS SISTEMI è un’azienda marchigiana specializzata nella produzione di centri di lavoro a CNC per svariate applicazioni, soprattutto verso il settore degli accessori moda. Per i suoi centri di lavoro l’azienda utilizza da circa dieci anni i controlli numerici Z32 di D.ELECTRON.