Takler rafforza la produzione e guarda al mercato globale
Takler ha investito nello stabilimento di Matera avviando una nuova linea di estrusione da 2.800 tonnellate. Ora l’azienda produce internamente i profili in leghe leggere utilizzati nella realizzazione di accessori e componenti per veicoli industriali. Lorenzo Lorusso, AD di Takler, spiega le opportunità aperte da questa integrazione a monte del processo produttivo
In Basilicata, nella zona industriale Jesce di Matera, si trova lo stabilimento della Takler Srl, che produce, distribuisce e vende componenti in acciaio e alluminio per il settore dei trasporti su ruota. Fondata nel 2005 dalla famiglia Lorusso, la Takler fa parte di un consolidato gruppo imprenditoriale che sin dal 1989 opera nel settore automotive. Già nel 2008 Takler inaugura una propria filiale tedesca per offrire un efficiente servizio logistico al nord Europa, e nel 2017 supera i confini europei con una filiale negli Stati Uniti. In poco tempo Takler diviene così un punto di riferimento per il settore dei veicoli industriali e commerciali. Oggi l’azienda conta su un portafoglio di oltre 2000 clienti in tutto il mondo grazie ad un solido know-how, alla grande attenzione agli sviluppi del mercato e alla ricerca di originali soluzioni decisive e affidabili. In questo quadro si innesta la scelta strategica nel 2019 di consolidare la struttura e il mix produttivo aziendale con l’installazione di una nuovissima pressa da estrusione da 2800 tonnellate, con l’obiettivo di produrre internamente i profili in alluminio impiegati nei prodotti. E’ ben noto che la necessità di alleggerire i mezzi di trasporto per cercare di ridurre i consumi ha reso l’alluminio un metallo molto utile sia nella produzione di elementi strutturali che di accessori. L’alluminio e sue leghe sono il futuro dell’industria dei trasporti e già oggi oltre un terzo di tutto il metallo leggero utilizzato in Europa, circa 14 milioni di tonnellate, è destinato alla mobilità. Parliamo oggi di questo nuovo impianto di estrusione e delle prospettive aperte da questo investimento con Lorenzo Lorusso, amministratore delegato di Takler.
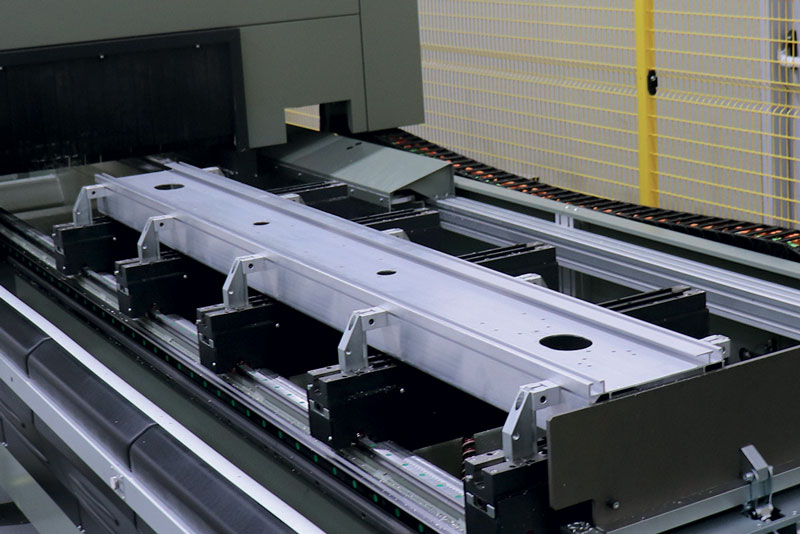
Takler è un’azienda giovane e molto dinamica e nasce dalla commercializzazione di accessori per automezzi. Oggi come siete strutturati?
La nostra azienda è nata per affermarsi nella produzione e distribuzione di componenti per l’industria dell’automotive e in particolare per il settore “Truck and Trailer”. In famiglia ci siamo distribuiti i compiti. Il primogenito Domenico Lorusso segue la divisione plastica come CEO di Lokhen, altra azienda del gruppo. Il secondogenito Giovanni segue la filiale americana Takler USA con l’incarico di CEO e il terzogenito Giuseppe è in Takler con il ruolo di Direttore Generale. La nostra esperienza consolidata negli anni nel settore unita alla nostra propensione a guardare sempre avanti verso nuove soluzioni e nuovi prodotti, ci ha convinto a sviluppare sempre più compiutamente il nostro ruolo di partner strategico all’interno del mercato in cui operiamo. Abbiamo quindi valutato a fondo le interessanti opportunità offerte dall’estrusione, per la molteplicità di forme e caratteristiche ottenibili. Non ci siamo accontentati di quanto reperibile sul mercato. Siamo consapevoli delle competenze acquisite e vogliamo proporre soluzioni originali ai nostri clienti o realizzarne di nuove in partnership con loro; ecco le ragioni per cui nel 2019 abbiamo deciso di investire anche noi nel settore dell’alluminio.
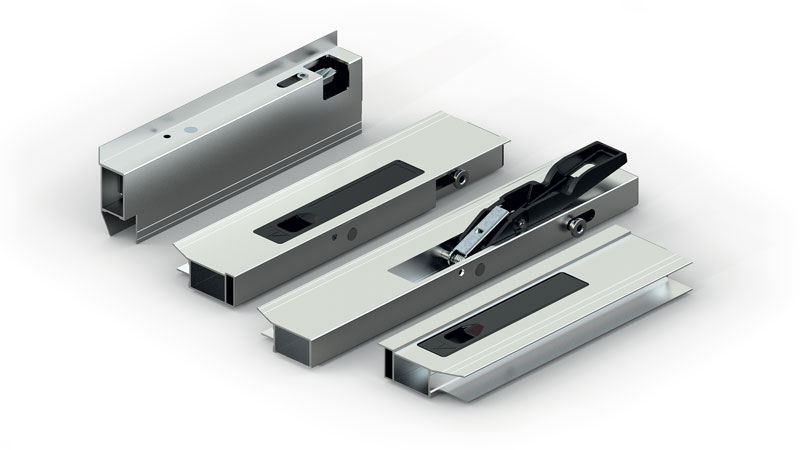
Iniziamo a parlare di numeri, potete darci indicazioni sul vostro fatturato, su come ha inciso la pandemia e qualche dato sul vostro nuovo impianto?
Dai 14 milioni di euro di fatturato nel 2020, quest’anno supereremo quota 32 milioni di euro di fatturato, un incremento di circa il 130%. Per il 2022 abbiamo a budget un’ulteriore crescita che ci dovrebbe portare sino a 50 milioni di euro, anche attraverso l’inserimento di nuovi prodotti sul mercato. Riguardo alla crisi legata alla pandemia, posso affermare che in realtà ha solo rallentato i tempi di realizzazione dei nostri progetti, incidendo marginalmente in una fase comunque positiva di crescita ben impostata e già a buon punto. Per quanto riguarda la struttura invece la nostra unità produttiva copre un’area complessiva di 30.000 metri quadrati di cui 14.000 coperti; occupiamo circa 90 persone includendo progettazione, produzione e vendita; a completamento della nostra produzione abbiamo disponibili centri di lavoro a cinque assi, per la lavorazione dei vari componenti. Riguardo infine alla nuova linea di estrusione, la capacità produttiva teorica della pressa può superare, a pieni turni e a pieno regime, le 15.000 tonnellate e quest’anno supereremo le 10.000 tonnellate. Mi permetta di esprimere un concetto che è alla base del nostro investimento: abbiamo deciso di dotarci di un impianto di estrusione di alluminio con i relativi centri di lavoro per servire i clienti del settore automotive, il nostro business di riferimento. Il nostro obiettivo è quello di poter produrre internamente molti dei prodotti che forniamo ai nostri clienti, passando dalla materia prima al prodotto finito, peculiarità questa che ci rende unici sul mercato. Non ci sono infatti altri produttori di accessori per i veicoli industriali e commerciali che abbiano anche un impianto di estrusione di alluminio al proprio interno. Noi abbiamo deciso di investire perché riteniamo che così facendo possiamo ampliare il catalogo offrendo nuovi prodotti ma anche controllare meglio il processo produttivo con un risultato molto più positivo sia per noi che per i nostri clienti in termini di qualità, affidabilità e prezzo.

Quali sono i prodotti che oggi realizzate, avete un catalogo ampio?
Abbiamo già a catalogo diverse centinaia di articoli progettati e prodotti da noi, come kit di protezione laterale “paraciclisti”, porte in alluminio, serie di sponde per le casse, scalette (queste anche in acciaio), paraurti, sistemi di montanti per sponde e altro ancora. In particolare la gamma di porte posteriori prende il nome di “Knock”, mentre i montanti in alluminio fanno parte della serie “Klever”. Le porte posteriori sono in realtà un elemento importantissimo per noi e per i nostri clienti. E’ chiaro che la chiave di volta per il successo e per la miglior penetrazione sul mercato interno e internazionale è nella progettazione e realizzazione di soluzioni vincenti, un lavoro esclusivo che è frutto delle conoscenze tecniche, dell’impegno e dell’esperienza del team di ingegneri che collaborano con noi. Oggi, a distanza di un paio di anni dall’installazione della pressa da estrusione, abbiamo già un’ampia offerta di soluzioni originali e innovative, in grado di esaltare le eccezionali doti di forma, di resistenza, di tenacità oltre che di estetica degli estrusi in alluminio. Siamo in pratica molto vicini alla totale copertura delle disponibilità di produzione e lavorazioni dei nostri impianti.
Parliamo allora più in dettaglio della pressa da estrusione e dell’impianto a valle
La macchina è una nuovissima SMS Omav da 2800 tonnellate, dotata di tutte le più moderne tecnologie. E’ in funzione dal 2019 e produce l’intera nostra gamma di profili a catalogo, che prima acquistavamo da altri estrusori, oltre ai nuovi profili richiesti dal mercato. La pressa è dotata di doppio puller e raffreddamento ad aria forzata e consente di realizzare profilati fino a una dimensione massima di 415 millimetri di larghezza e 14 metri di lunghezza. Il banco di estrusione con rulli in kevlar, il forno d’invecchiamento, la stiratrice e tutto l’impianto sono stati studiati per garantire queste caratteristiche per estrusi di alta qualità. Importante citare tra i nostri prodotti i monoprofili sponda da 415 millimetri di nostro design, che completano in modo importante la nostra gamma di prodotti. È significativo sottolineare che con il nostro impianto, con le conoscenze pregresse e con la creatività e flessibilità che ci caratterizza, siamo in grado di soddisfare praticamente ogni tipo di richiesta utilizzando principalmente le tipiche leghe 6060, 6063, 6005 e loro varianti.

In quali mercati operate?
Storicamente l’export è sempre stato per noi il mercato principale. Prima del 2019 circa l’80% della nostra produzione era rivolta all’estero, in Germania in particolare ma anche in altri paesi in Europa ed extra europei. Ricordo ancora che per agevolare la distribuzione dei nostri prodotti all’estero, abbiamo aperto due filiali: una ad Ulm in Germania e l’altra, creata nel 2017 negli Stati Uniti, si trova nel New Jersey presso New York. I due hub sono utilizzati sia per l’assemblaggio finale dei prodotti che come depositi di prodotti finiti.
Per la progettazione come siete organizzati?
Come detto, abbiamo disponibili a catalogo centinaia di componenti da noi progettati. I vari prodotti vengono forniti solitamente in kit di assemblaggio e ci riserviamo la possibilità di fornire ricambi in post vendita. Nella realizzazione dei nostri articoli è molto importante l’attività di ricerca e sviluppo. Per questo motivo nel 2018 abbiamo creato all’interno del nostro gruppo una nuova società, la TKL, formata esclusivamente da ingegneri dedicati allo studio e alla progettazione di nuove soluzioni per prodotti già esistenti o per nuove realizzazioni. Proprio per la natura della sua attività, TKL collabora con il Politecnico di Bari che da tempo opera con il nostro Gruppo. La progettazione richiede naturalmente il rispetto delle omologazioni necessarie alla commercializzazione dei nostri prodotti, per questo Takler ha ottenuto tra le altre, la certificazione UNI EN 12642 XL per le porte. Tutti i manufatti da noi studiati e realizzati vengono sottoposti a specifici collaudi tramite enti certificati, sia in Italia che all’estero; cito l’ultimo effettuato sulle porte Knock, sottoposte a una prova di resistenza a 32 tonnellate. Molte delle soluzioni e degli articoli progettati sono stati brevettati, e questo ci rende sicuramente orgogliosi in quanto garanzia di un importante valore aggiunto da presentare ai nostri clienti sul mercato.

Fate molta comunicazione tecnico-informativa, partecipate a manifestazioni internazionali di settore?
In questo momento stiamo realizzando nuovi prodotti che presto presenteremo a importanti manifestazioni espositive internazionali. Recentemente, dal 30 settembre al 3 ottobre scorsi, eravamo presenti in Germania alla NUFAM Karlsruhe. Dal 16 al 20 novembre parteciperemo a SOLUTRANS a Lione, nel 2022 dal 20 al 25 settembre saremo ad Hannover all’importante manifestazione internazionale IAA. Stiamo attualmente valutando la partecipazione ad altre fiere importanti anche in Italia.
Concludiamo con uno sguardo al futuro, alle prospettive che vi attendete nei prossimi anni, e alle iniziative di sviluppo che avete messo in cantiere.
Per definizione le aziende devono pensare al futuro e non vivere solo di presente; per noi quindi il paradigma di vita è la crescita, una dinamica continua alla ricerca del miglior mix produttivo e di vendita, dalle tecnologie ai mercati, all’organizzazione interna, alla Ricerca & Sviluppo, all’inserimento dell’impresa nel contesto sociale del territorio in cui opera. Per noi la programmazione del futuro dell’impresa è parte rilevante del quotidiano, esemplare il caso che ha offerto l’occasione di questo incontro e cioè la decisione di entrare nel mondo dell’estrusione, scegliendo l’autonomia produttiva per la realizzazione dei prodotti che presentiamo sul mercato. Il gruppo Takler è presente sul mercato da poco più di 15 anni. Siamo quindi relativamente giovani ma abbiamo già la giusta maturità per poter fare dei nuovi passi in avanti. Le giovani generazioni presenti in azienda, a cominciare dai miei figli fino a tutti i collaboratori, mi danno l’entusiasmo giusto per guardare al futuro con nuovi progetti, nuove iniziative e nuovi investimenti.