High Precision Under the Highest Pressures
SACMI Imola is part of SACMI Group, a producer and marketer of manufacturing plants and industrial technology for the ceramic and packaging sectors. A company’s Division produces presses for metal powder, a market in which SACMI is one of the top brands. By monitoring the synchronized movement of hydraulic axis, Temposonics® position sensors from MTS Sensors play an important role in achieving uniformity and a consistent level of quality in production.
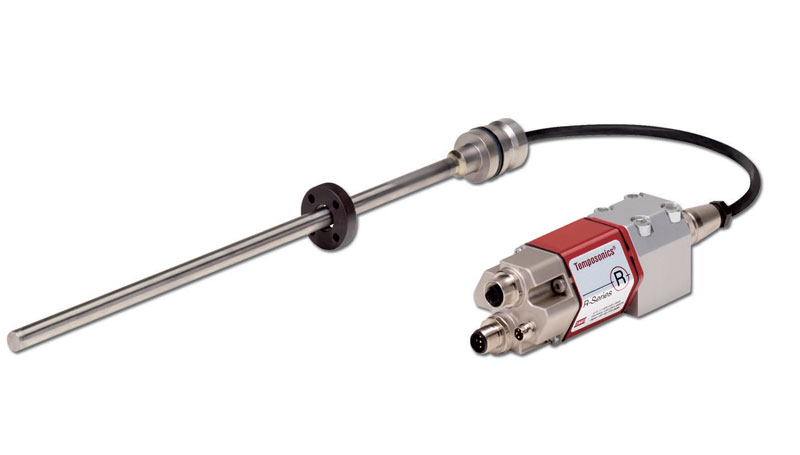
Parts made from metal powder are very common, especially in the automotive industrial sector. Here, gears, pumps, pulleys and many other components are often made from metal powder instead of forged or cast metal.
Davide Foschi, Technical Manager of Advanced Technologies B.U.at SACMI explains how position transducers can support the operation of metal powder presses: “The use of metal powder parts is not confined to gears, pumps and pulleys, but it also involve power tools and home appliances. The reason is quite simple. Parts made from metal powder are a cost-effective and reliable alternative when compared to machined, forged or cast parts. You pour the powder into the mould, press it into shape with high pressure and then run the finished part through a furnace so that the metal powder particles sinter and keep the pressed shape.” The advantage of the metal powder presses is that they can process more than twenty items per minute, which means that this process is a lot faster and more efficient than casting metal into shape. In most of the applications pressed metal powder is therefore an ideal and cost effective option.
Monitoring the synchronized movement of hydraulic axis
Although, there are also electric metal powder presses, the main portion of pressed automotive parts are made by fully automated hydraulic CNC presses. Sacmi presses operate with high forces up to 1,000 tons and that is a level very far from the one that electric presses can reach. The Temposonics® R-Series position sensors are important components of hydraulic presses. For almost every movement in the press there is one position sensor which helps to control movement. Mr Foschi continues: “Let me illustrate how crucial the sensors are for our machines: we produce metal powder presses with about ten hydraulic axes per press. All these axes must work synchronically to achieve uniformity and a consistent level of quality of the finished product. Therefore, they are controlled with the help of ten MTS Sensors position sensors because they match the high precision and quality SACMI guarantees to its customers.”
Ease of installation and reliable position measurement
The cooperation between SACMI and MTS Sensors began more than twenty years ago and originally the sensors were used for ceramic presses and other business areas. When SACMI started producing metal powder presses, it turned to the Temposonics R-Series because of the good experiences they previously made and the sensor varieties that MTS Sensors could offer. The issue with the presses is that though they can be gigantic, they must be built compactly to save space but still manage even 1,000 tons of force. SACMI chose the R-Series RD4 position sensor with EtherCat for their presses because they were space saving in the application. Another advantage of the R-Series family member is that the electronics are detached and can be placed elsewhere in the system due to a shielded cable that connects the sensor with the electronics. In this way the sensor itself takes up less space in the cylinder of the hydraulic axis, while the signal quality of the position sensor remains intact, precise and reliable for an easy control of the automated pressing processes of the system. Another important advantage of the RD4 series is the possibility to install the sensor directly inside the hydraulic piston. This leads to a very direct and precise measurement, and it is not influenced by the elastic deformations enabling a very effective control of the movement.
Furthermore, the RD4 sensor also enabled the company to avoid another issue: high temperature on the electronics. When a sensor with electronics is integrated into a hydraulic axis it can happen that when the oil heats up, the sensor and its electronics do too. When the temperature gets too high, the electronics could start to fail or delay the measurement. With the RD4, this issue is avoided because of the detached electronics which, with a shielded cable, enables reliable position measurement with electronics elsewhere. “A big advantage is that we are able to work closely together with MTS Sensors to continuously optimize the sensor integration in our presses,” says Mr. Foschi. “In the beginning we had the issue that, while the sensors were ideal for limited spaces in the hydraulic cylinders, there were too many cables as each sensor required one connection. So, we sat down with MTS Sensors and found a solution for this issue and now we are able to read all sensors with one single cable.”
Close cooperation for future projects
The strong and decades-long relationship between SACMI and MTS Sensors provides them with a good standing when it comes to future projects.
The whole industry is currently on the move and changing or updating. When it comes to concrete examples about implementing Industry 4.0 or predictive maintenance and condition monitoring, Sacmi provides users with all necessary data from sensors applied throughout the metal powder presses. “Providing all this data to our customers – Mr. Foschi concludes – helps them to keep an eye on their production process and set up maintenance schedules based on the information we provide. Hereby, the Temposonics® position sensors are part of a complex monitoring system that covers among other things the oil temperature, the cooling system, and the piston movement.”