MEGA Synchro: per una maschiatura rigida e sincronizzata
Per eseguire una maschiatura di precisione esistono tecnologie alternative all’utilizzo dei portapinze, capaci di attenuare il carico sul maschio assorbendo l’errore di sincronizzazione. Parola di BIG DAISHOWA.
di Alberto Marelli
La maschiatura è una tipologia di lavorazione meccanica che crea non poche difficoltà. I problemi che pone sono noti e tuttora insidiosi, nonostante l’introduzione di nuove tecnologie e attrezzature. Negli anni Ottanta il metodo più diffuso era quello della maschiatura in trazione-compressione. Ciò comportava l’aggiunta di molle ai portamaschi, così da permettere al maschio di entrare e uscire dal foro in modo autonomo; questo processo poteva però essere eseguito soltanto a velocità di rotazione estremamente ridotte. Negli anni successivi, i costruttori di macchine hanno sviluppato tecnologie che hanno contribuito ad automatizzare il processo di maschiatura, riducendo le difficoltà per gli operatori di macchina.
Sincronizzazione, usura e scelta degli utensili
Oggi, la maggior parte delle macchine utensili a controllo numerico opera a cicli fissi che permettono di accoppiare i codici M e i codici G così da sincronizzare in modo preciso il mandrino e l’asse di avanzamento per la massima ripetibilità, realizzando una maschiatura rigida e sincronizzata.
Gli encoder integrati possono addirittura controllare questo aspetto del processo e regolare la macchina così da mantenere la correlazione ideale tra avanzamento e velocità. Grazie a questi progressi tecnologici, le macchine possono oggi effettuare maschiature con velocità del mandrino anche oltre i 4.000 giri/min. Nonostante ciò, però, l’usura del maschio, il passo e la tolleranza del filetto e, cosa ancor più importante, il rischio di rottura dei maschi, sono tutti aspetti che condizionano la lavorazione prolungandone la durata e influenzandone in modo negativo l’efficienza. Indipendentemente dalle migliorie tecnologiche apportate alle macchine utensili, ancor oggi risulta molto difficile sincronizzare la profondità (soprattutto nel caso di fori ciechi) e il passo del filetto con l’improvviso arresto e inversione di rotazione del maschio.
Questo aspetto introduce una nuova variabile di fondamentale rilevanza per un’esecuzione perfetta della lavorazione, oltre all’affidabilità della macchina: gli utensili. “Quando si tratta di maschiatura – spiega Giampaolo Roccatello, Chief Sales and Marketing Officer Europe di BIG DAISHOWA Europe – la scelta ricade di solito sui portapinze, perché sono facili da regolare e ben bilanciati, e capaci di offrire un’elevata precisione di concentricità. Quello di cui però molte officine non si rendono conto è che la rigidità dei portapinze, che è uno dei loro punti di forza, può rappresentare un problema nel caso della maschiatura. La rigidità non è in grado di contrastare le spinte assiali estreme cui sono sottoposti il maschio e il pezzo, accentuando quegli aspetti critici che sono il processo di arresto e movimento a ritroso e il mantenimento della sincronizzazione”.
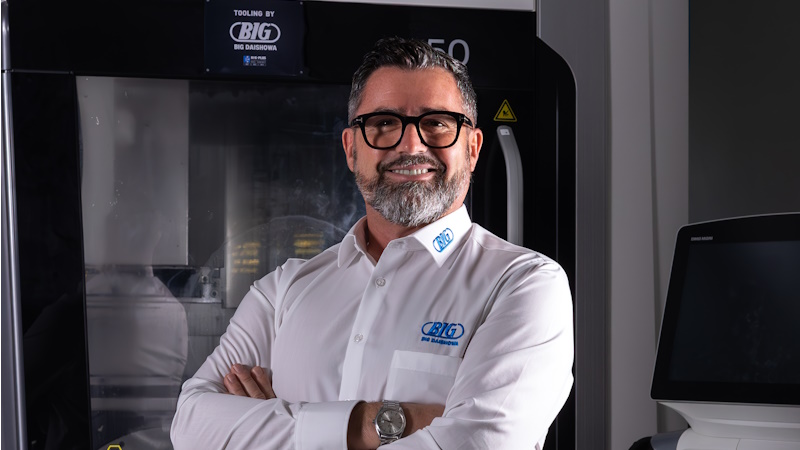
MEGA Synchro: minore scheggiatura e quindi ridotta usura del maschio
Analizziamo un esempio concreto. Utilizzando un dinamometro, BIG DAISHOWA ha misurato il carico di spinta esercitato su un maschio per filettare fissato su un portapinze in alluminio con velocità di avanzamento 20 m/min, regime di rotazione 1.050 giri/min e profondità 12 mm. All’inizio dell’inversione della rotazione, il carico era di circa 75 kg.
“È la conseguente pressione assiale che comporta la rottura del maschio, la sua durata limitata e filettature imprecise”, afferma Roccatello. “Se da un lato è facile intuire che la compromissione o rottura dei maschi e la scarsa qualità della filettatura comportano conseguenze fatali in termini economici, dall’altro occorre tener presente che ridurre la velocità del mandrino non è la soluzione corretta per ottenere risultati ottimali in termini di produttività e durata degli utensili. I costruttori di macchine hanno contribuito a semplificare il processo di maschiatura, e la stessa cosa fanno i costruttori di utensili. Esistono infatti portamaschi progettati specificatamente per ridurre il carico di spinta imposto al maschio e assorbire l’errore di sincronizzazione”.
Per esempio, il sistema portamaschi MEGA Synchro di BIG DAISHOWA prevede il fissaggio al corpo con un bullone a croce, che passa attraverso l’esterno della cavità e attraverso l’adattatore, bloccandolo in posizione. Il foro che ospita il bullone ha un adattatore sincronizzato, ovvero una boccola in elastomero che ammortizza il bullone. Il rapporto tra la boccola e il bullone assicura lo spazio necessario ad ammortizzare la spinta.
“L’ammortizzazione avviene non soltanto nella parte inferiore del foro quando la torsione viene invertita, dove rigidità e picchi di forze possono portare alla rottura del maschio, ma durante l’intero processo di taglio”, sottolinea Roccatello. “Questo comporta un maggior controllo del passo e della tolleranza del filetto eliminando la fase di taglio in uscita anche nel caso di macchine con momenti torcenti ad alta velocità. La riduzione del carico di spinta implica anche una minore scheggiatura e quindi usura del maschio, indipendentemente dall’angolo del filetto, allungandone la durata anche del doppio”.
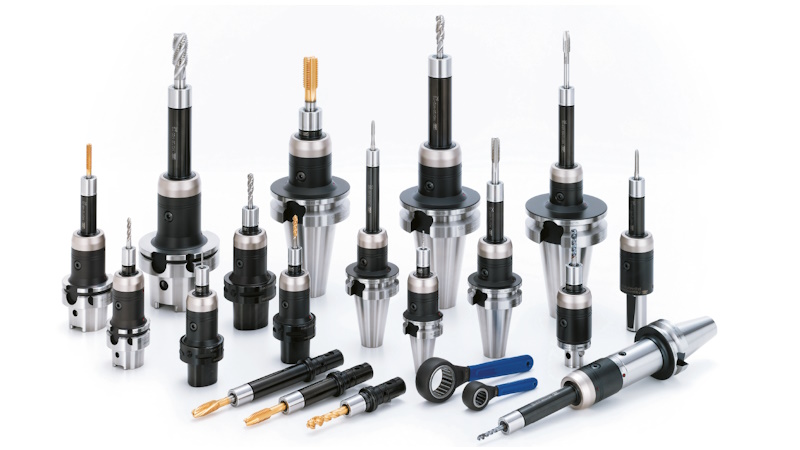
MEGA Syncro è perfetto per la maschiatura rigida ad alte prestazioni
Quanta forza è in grado di assorbire il sistema di ammortizzazione del portamaschio? Utilizzando il dinamometro per misurare la forza a parità di condizioni e sostituendo il portapinze con il mandrino di maschiatura MEGA Synchro, il carico massimo rilevato era di circa 6 kg, ovvero almeno dieci volte minore.
“Fortunatamente oggi le officine possono contare su macchine CNC tecnologicamente avanzate che permettono di eseguire lavorazioni complesse, però questo non basta. È necessario utilizzare i portautensili appropriati per ottimizzare l’efficienza della macchina e compensare gli errori di sincronizzazione che sono impossibili da evitare. Esistono alternative alle vie tradizionali come quella che prevede l’utilizzo di un portapinze per la maschiatura, tutto a beneficio della precisione, produttività e redditività della lavorazione.
Il sistema MEGA Synchro è perfetto per la maschiatura rigida ad alte prestazioni sulle macchine CNC, riducendo il carico al maschio di oltre il 90%”, conclude Roccatello.
Il sistema è dotato di 41 corpi e 45 portamaschi (per diverse tipologie di attacco) e offre lunghezze di protezione indicate per qualsiasi macchina; supporti maschio corti, medi e lunghi sono standardizzati per coprire campi di maschiatura da M1 a M36. La qualità della filettatura e la durata dell’utensile risultano migliorati grazie alla riduzione dei carichi di spinta causati dagli errori di sincronizzazione durante la maschiatura rigida. Il refrigerante è fornito sia attraverso l’utensile sia periferico, e anche contemporaneamente. Le scanalature spiralate sul maschio generano un carico al maschio durante l’inversione della velocità, similmente a quanto accade in fresatura.
Inoltre, il sistema Drill Tapper garantisce prestazioni elevate per le applicazioni manuali ed è un sistema esclusivo di foratura e maschiatura. Questo portautensili a cambio rapido permette di passare dai maschi alle punte in pochi secondi, consentendo due operazioni con una testa stabile.
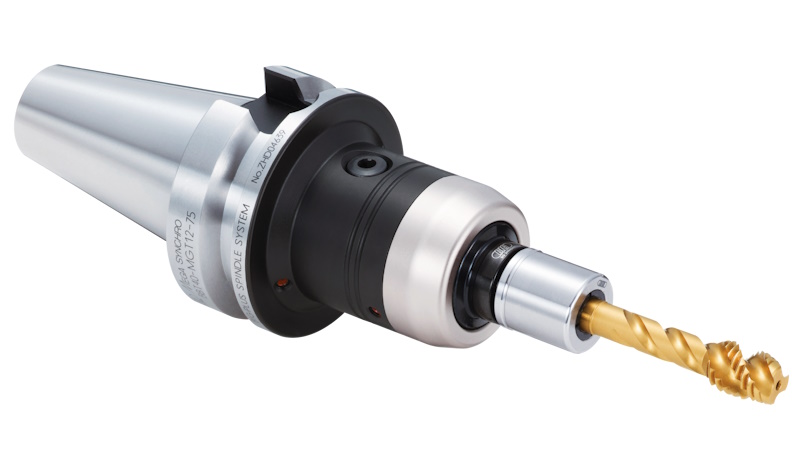
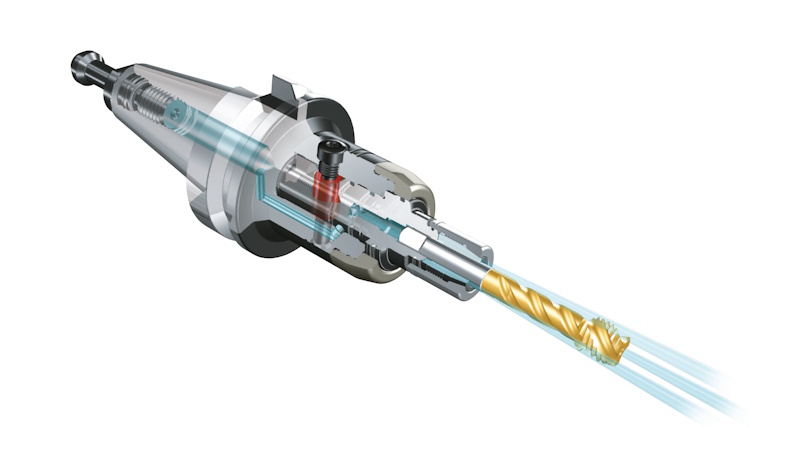
Potenziate le attività in Europa
BIG DAISHOWA punta ad accelerare l’innovazione e l’efficienza operativa attraverso la riorganizzazione strategica delle attività europee. Questa iniziativa include il rebranding in BIG DAISHOWA Europe, che così allinea la filiale europea alla casa madre, e prevede importanti investimenti in ricerca, logistica e produzione.
Dal 1° gennaio di quest’anno, il produttore di utensili ha modificato il proprio nome in BIG DAISHOWA Europe (ex BIG KAISER Europe). Questo cambiamento mira a uniformare il marchio dell’azienda a livello globale, rafforzandone la posizione sul mercato.
Gli sviluppi principali includono:
– Hub europeo di Ricerca e Sviluppo. Il Centro di Ricerca e Sviluppo di Rümlang, in Svizzera, diventerà il centro di eccellenza globale del Gruppo BIG DAISHOWA, concentrandosi sulla digitalizzazione e sull’automazione degli utensili.
– Ottimizzazione della produzione globale. La produzione degli utensili di barenatura verrà trasferita in Giappone, mentre l’assemblaggio e l’assistenza per i clienti europei resteranno in Svizzera.
– Potenziamento delle operations in Europa. Nel 2026 verranno realizzati in Germania il nuovo headquarter europeo e il centro logistico europeo di BIG DAISHOWA, che consolideranno il servizio ai clienti e l’efficienza operativa.
Il Centro di Ricerca e Sviluppo europeo di BIG DAISHOWA si concentrerà sullo sviluppo di utensili digitali all’avanguardia, che comprendono le teste di barenatura digitali EWE e le teste di barenatura automatiche EWA, consolidando il ruolo centrale della Svizzera nel progresso delle tecnologie di utensili di precisione.