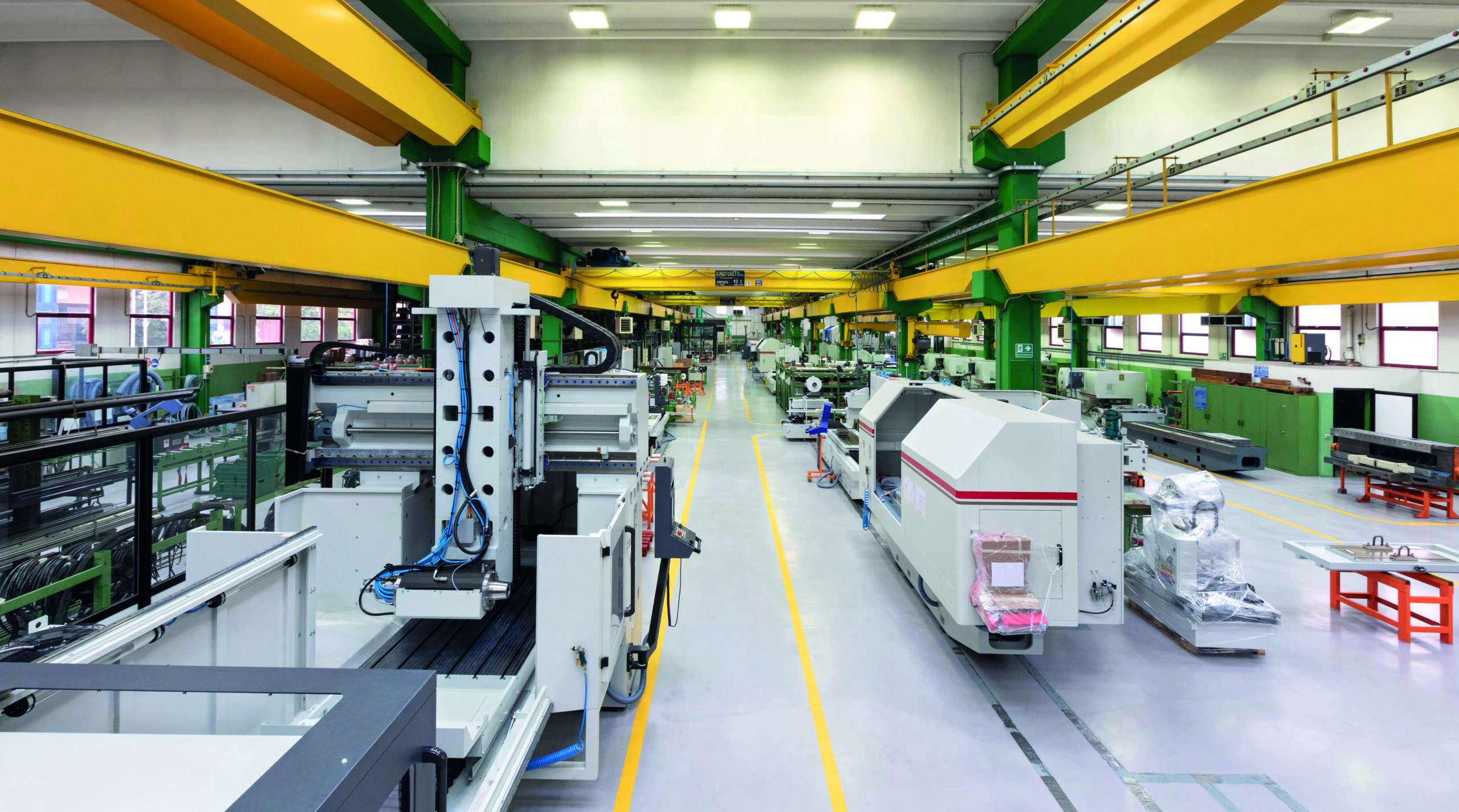
Dalla progettazione alla produzione, in Rosa Ermando nulla è lasciato al caso. Ogni rettificatrice è il risultato di un processo produttivo altamente verticalizzato, che garantisce un controllo totale su qualità, tempi e costi, diventando il cuore del progetto GrindTech.
di Adriano Moroni
Partiamo da un presupposto: quando si parla di rettifica, la precisione e la qualità delle lavorazioni che una macchina è in grado di garantire sono fattori determinanti. Ma precisione e qualità non sono il frutto del caso, bensì il risultato di un processo rigoroso che in Rosa Ermando parte dalla progettazione e dalla costruzione della meccanica, elemento essenziale di ogni macchina.
Questa è una delle ragioni per cui, nell’azienda lombarda nota in tutto il mondo per le sue rettificatrici tangenziali a marchio Rosa GrindTech e Favretto GrindTech, tutte le fasi critiche e strategiche del processo produttivo vengono gestite internamente, così da garantire un controllo pressoché totale su qualità, tempi e costi.

Forte verticalità
Lo ha spiegato bene Andrea Portosa, COO dell’azienda di Rescaldina, provincia di Milano, quando lo abbiamo incontrato. “Uno dei principali punti di forza di Rosa Ermando è sempre stata la capacità di realizzare soluzioni tecnologiche che fossero, di fatto, il risultato dell’interpretazione delle esigenze produttive degli utilizzatori”, ci ha detto Portosa.
“Il nostro valore aggiunto, però, è dato anche e soprattutto dall’essere riusciti a mettere a punto un modello produttivo molto verticalizzato, che si traduce in un controllo estremamente rigoroso e approfondito di tutte le fasi di costruzione delle nostre macchine. Partiamo dalla ghisa dei basamenti, fusa in una fonderia in Romania partecipata da Rosa Ermando SpA, per poi passare alle fasi di lavorazione, assemblaggio (meccanico ed elettrico) e collaudo, che si svolgono interamente nel nostro stabilimento di Rescaldina. Questo ci consente di mantenere un controllo totale sull’intero processo, assicurando l’elevata qualità delle nostre soluzioni, che il mercato da sempre ci riconosce”.

Tecnologia al servizio della qualità
Nello stabilimento Rosa Ermando di Rescaldina, nulla viene lasciato al caso. Tutto è ordinato, pulito, preciso e pensato in ogni minimo dettaglio. Costruito su un’area di 6.000 m2 e con una capacità produttiva di 50-60 macchine all’anno, questo sito è un concentrato di tecnologia avanzata, sostenibilità ambientale e sicurezza dei lavoratori, che ben si integrano con un sistema gestionale all’avanguardia, conforme agli standard dell’Industria 4.0.
Parte integrante di questa filosofia è l’aggiornamento costante del parco macchine, attraverso interventi di retrofit e investimenti mirati che assicurano una tecnologia sempre giovane ed efficiente. Questa attenzione alla modernizzazione tecnologica è accompagnata da una grande valorizzazione delle risorse umane: l’aggiornamento continuo delle competenze tecniche del personale, dai progettisti agli operatori specializzati, rappresenta infatti un altro pilastro fondamentale della strategia aziendale.
Per tutte le esigenze
Il tempo necessario per realizzare una rettificatrice tangenziale Rosa GrindTech o Favretto GrindTech varia in base alla tipologia e complessità del modello.
“Il cliente può scegliere il modello di rettificatrice da uno dei nostri cataloghi, che offrono gamme standard, pensate per soddisfare diverse esigenze industriali, con la possibilità di richiedere personalizzazioni mirate per adattare la macchina a specifiche necessità operative”, ha affermato Portosa. “Forniamo, ad esempio, attrezzature speciali per la presa del pezzo, progettate per essere installate sulla tavola e garantire il bloccaggio sicuro di particolari meccanici complessi non previsti nella configurazione standard. Inoltre, possiamo integrare accessori personalizzati sulla testa della macchina, come portamole speciali o utensili sviluppati per lavorazioni non standard, ideali per ottenere finiture di alta precisione o per l’utilizzo di mole specifiche”.
Il processo produttivo, cuore del progetto GrindTech, privilegia qualità ed efficienza pur garantendo tempi di esecuzione delle commesse sempre in linea con le richieste del mercato. In Rosa, infatti, la produzione in serie di componenti comuni a più linee di produzione garantisce tempi ridotti di approntamento delle macchine. L’evoluzione in chiave 4.0, completata nel 2019, ha consentito inoltre di perfezionare il sistema di monitoraggio in tempo reale dei sistemi di produzione, potenziando la capacità di analisi e ottimizzazione dell’intero processo.


Dalla progettazione alle materie prime
È Maurizio Ballabio, Responsabile di produzione dell’azienda, a farci entrare nel vivo del processo produttivo, che oggi rappresenta il cuore del progetto GrindTech.
“Tutto ha inizio con la progettazione, durante la quale i nostri tecnici specializzati progettano le macchine per garantire prestazioni elevate e affidabilità nel tempo. È in questa fase che vengono definiti con precisione i materiali, le tolleranze e i processi di lavorazione, tenendo conto delle condizioni operative a cui le rettificatrici saranno sottoposte. Questo approccio preventivo riduce al minimo i difetti e ottimizza l’efficienza dell’intero ciclo produttivo”, ci ha raccontato Ballabio.
Dopo la progettazione, si passa alla selezione delle materie prime e dei componenti. “Le fusioni di ghisa delle strutture, elemento chiave per la stabilità della macchina, sono prodotte in una fonderia partecipata, capace di realizzare pezzi di grandi dimensioni – fino a 15 m di lunghezza in un unico blocco – il che ci permette di avere un controllo diretto e costante su questo componente essenziale”, ha spiegato Ballabio.
In parallelo, i componenti realizzati da fornitori esterni vengono forniti con un protocollo di collaudo e un certificato di conformità alle specifiche richieste. Questo approccio, unito a collaborazioni consolidate con fornitori storici, consente di mantenere un controllo rigoroso sulla qualità lungo tutta la filiera. “È un po’ come se, di fatto, avessimo integrato nel nostro processo alcuni fornitori strategici, capaci di aggiungere ulteriore valore ai nostri prodotti”, ha sottolineato Ballabio.

Standard di eccellenza
Ogni fase di lavorazione viene gestita internamente nello stabilimento di Rescaldina, dai componenti più piccoli alle strutture principali delle rettificatrici, grazie a un parco macchine in grado di lavorare pezzi di grandi dimensioni, fino a 12 m di lunghezza e 3 m di larghezza.
“I componenti più critici, identificati sin dalla fase progettuale, sono sottoposti a controlli rigorosi al 100%, grazie all’ausilio di macchine di misura avanzate”, ha spiegato Ballabio. “Ogni pezzo è accompagnato da un protocollo di collaudo dettagliato che documenta tutte le verifiche effettuate lungo il processo produttivo. Questo garantisce la conformità alle normative ISO e il mantenimento degli standard di eccellenza”.
L’assemblaggio, meccanico ed elettrico, è il momento in cui la visione progettuale prende forma concreta, dando vita a macchine robuste, affidabili e progettate per durare nel tempo.
“Il nostro processo produttivo è ottimizzato per la produzione in serie, con componenti realizzati in lotti da 40-50 pezzi, indipendentemente dal modello di macchina”, continua Ballabio. “Questi lotti vengono stoccati nel magazzino centrale, pronti per l’assemblaggio. Quando riceviamo un ordine, viene generata una distinta di prelievo con l’elenco di tutti i materiali necessari, che vengono prelevati e posizionati su scaffali dedicati insieme ai gruppi preassemblati. Questo consente ai montatori un accesso immediato ai componenti, ottimizzando il flusso di lavoro, riducendo i tempi di attesa e migliorando l’efficienza nella costruzione delle macchine”.
La qualità è nei dettagli
C’è una fase cruciale nella produzione delle macchine utensili chiamata raschiettatura, il cui scopo è migliorare la planarità e l’estetica di superfici già parzialmente lavorate. Si tratta di una lavorazione meccanica di finitura superficiale, eseguita asportando il materiale in eccesso dalla superficie da lavorare con degli appositi raschietti. Questa operazione è particolarmente importante nella costruzione delle rettificatrici, dove un accoppiamento ottimale tra il basamento e la tavola è essenziale per garantire la precisione della macchina. Affinché ciò sia possibile, le due superfici devono essere perfettamente aderenti.
“Per eseguire la raschiettatura, si parte da una superficie di riferimento, colorata con un pigmento speciale chiamato blu di Prussia”, ci ha spiegato Maurizio Ballabio, Responsabile di produzione di Rosa Ermando. “Questo pigmento viene applicato per evidenziare i punti di contatto quando un’altra superficie viene appoggiata su quella di riferimento, affinché mostrino con precisione le aree in cui il materiale deve essere rimosso. In questo modo, con l’ausilio di un raschietto manuale, l’operatore interviene sui punti più alti, asportando il materiale in eccesso con movimenti accurati. Questo processo viene ripetuto più volte, fino a ottenere una perfetta conformità tra le due superfici, garantendo così un accoppiamento ottimale”.
In Rosa la raschiettatura è eseguita interamente a mano. Questa competenza artigianale permette di raggiungere un livello di precisione che nessuna tecnologia moderna è in grado di eguagliare. La qualità della raschiettatura si riflette direttamente sulla precisione e sull’affidabilità delle lavorazioni successive, rappresentando un vero e proprio valore aggiunto per le macchine prodotte.
